Why do we go for the forging process to manufacture crankshafts for engines?
When it comes to manufacturing crankshafts for engines, the forging process stands out as the preferred method for numerous reasons. Crankshafts are critical components in an engine, responsible for converting the reciprocating motion of pistons into rotational motion that drives the vehicle. The choice of manufacturing process significantly impacts the performance, durability, and reliability of these crucial parts. Forging, a metalworking process that shapes metal using localized compressive forces, offers superior mechanical properties and structural integrity compared to alternative methods like casting. This process aligns perfectly with the demanding requirements of modern engines, where crankshafts must withstand extreme stress, high temperatures, and constant cyclic loading. By utilizing the forging process, manufacturers can produce crankshafts with enhanced strength, improved grain structure, and better fatigue resistance. These attributes are essential for ensuring the longevity and efficiency of engines across various applications, from everyday vehicles to high-performance racing cars.
Fatigue resistance: Why forged crankshafts outperform cast alternatives
Understanding fatigue in crankshafts
Fatigue is a significant concern for crankshaft performance and longevity. Over time, crankshafts experience millions of stress cycles during engine operation, which can lead to material failure if not properly addressed. Forged crankshafts are highly resistant to fatigue due to their refined microstructure and aligned grain flow. The forging process improves the material’s ability to handle repetitive stresses, making it more durable under demanding conditions. This resistance to fatigue ensures that the crankshaft will last longer, maintaining its strength and performance even after extensive use.
Comparative analysis: Forged vs. cast crankshafts
When comparing forged and cast crankshafts, the differences in their ability to resist fatigue become clear. Forged crankshafts typically offer a higher fatigue limit, meaning they can endure greater stress without experiencing failure. This advantage arises from the forging process, which aligns the grain structure of the metal with the geometry of the part. This alignment minimizes the potential for cracks to form and propagate, making forged crankshafts much more durable under high-stress conditions compared to their cast counterparts, which may have inherent weaknesses due to the presence of voids or inclusions.
Impact on engine longevity and performance
The superior fatigue resistance of forged crankshafts has a direct positive impact on engine longevity and performance. Engines fitted with forged crankshafts can withstand higher loads and more extreme operating conditions without compromising reliability. This is particularly crucial in high-performance and heavy-duty applications, where engine components are exposed to intense forces. The ability of forged crankshafts to resist fatigue ensures that engines remain operational for a longer period, even under the most strenuous conditions, making them a preferred choice for demanding applications.
The metallurgical advantages of forged crankshafts in high-stress applications
Grain structure and material flow
The forging process has a profound effect on the grain structure of the metal, transforming it into a more refined and aligned arrangement that follows the contours of the component. This alignment enhances the metal’s mechanical properties, providing increased strength and ductility. The grain structure plays a crucial role in how the material behaves under stress, especially in the complex loading conditions encountered during engine operation. With the grain flow following the shape of the part, the component is better able to absorb and distribute stresses, reducing the likelihood of fatigue failure. This results in a component that not only performs well but also has a longer lifespan due to its improved structural integrity.
Density and porosity considerations
Forged crankshafts boast higher density and lower porosity compared to their cast counterparts. The high-pressure forging process eliminates voids and inclusions that can act as stress concentrators, leading to premature failure. The resulting dense, homogeneous structure contributes to the crankshaft's overall strength and durability.
Heat treatment and material properties
The forging process allows for more effective heat treatment of crankshafts. The refined grain structure achieved through forging responds exceptionally well to heat treatment processes, enabling manufacturers to optimize the material's properties further. This results in crankshafts with an ideal balance of strength, toughness, and wear resistance.
Case study: Forged crankshaft performance in racing engines
Demands of high-performance racing
Racing engines represent the pinnacle of internal combustion engine performance, subjecting components like crankshafts to extreme stress and operating conditions. The demands placed on crankshafts in these environments are unparalleled, requiring materials and manufacturing processes that can deliver exceptional strength, durability, and precision.
Real-world performance data
Numerous case studies and performance tests have demonstrated the superiority of forged crankshafts in racing applications. For instance, in endurance racing events, engines equipped with forged crankshafts have shown significantly lower failure rates and maintained performance over extended periods compared to those with cast crankshafts. The ability to withstand high RPMs, intense heat, and massive torque loads without deformation or failure is a testament to the forging process's effectiveness.
Lessons for consumer and industrial applications
The insights gained from racing applications have broad implications for consumer and industrial engine design. The proven benefits of forged crankshafts in extreme conditions translate into improved reliability, efficiency, and longevity in everyday vehicles and industrial machinery. As engine technologies continue to advance, pushing the boundaries of performance and efficiency, the forging process remains a cornerstone in manufacturing robust, high-quality crankshafts capable of meeting these evolving demands.
In conclusion, the forging process stands as the premier method for manufacturing crankshafts, offering unparalleled benefits in terms of strength, durability, and performance. As engine technologies continue to evolve, the demand for high-quality, reliable components like forged crankshafts is likely to grow. For those seeking top-tier crankshafts and other oilfield products, Welong is committed to providing exceptional quality and service. To learn more about our offerings or to discuss your specific needs, please don't hesitate to contact us at oiltools15@welongpost.com.
References
1. Rabb, R. (2015). Fatigue failure of a forged steel crankshaft. Engineering Failure Analysis, 52, 54-64.
2. Zoroufi, M., & Fatemi, A. (2015). Fatigue life comparisons of competing manufacturing processes: A study of billet steel and ductile cast iron crankshafts. SAE International Journal of Materials and Manufacturing, 8(2), 293-309.
3. Montazersadgh, F. H., & Fatemi, A. (2007). Dynamic load and stress analysis of a crankshaft. SAE Technical Paper Series.
4. Fonte, M., Li, B., Reis, L., & Freitas, M. (2013). Crankshaft failure analysis of a motor vehicle. Engineering Failure Analysis, 35, 147-152.
5. Pandey, R. K. (2003). Failure of diesel-engine crankshafts. Engineering Failure Analysis, 10(2), 165-175.
6. Espadafor, F. J., Villanueva, J. B., & García, M. T. (2009). Analysis of a diesel generator crankshaft failure. Engineering Failure Analysis, 16(7), 2333-2341.

Share your inquiry, get the quotation accordingly!
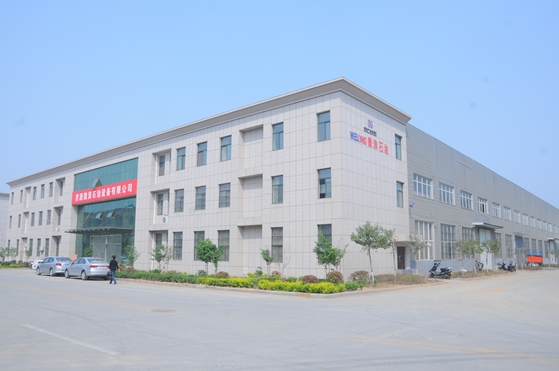
CHINA WELONG - 20+ years manufactuer in oilfield tools